What do chisels, planes, spoke shaves, gouges, marking knives, etc. all have in common? Easy – a sharp edged blade made of steel. After sharpening my own chisel and plane collection and reading advertising and product reviews for woodworking blades, I began to wonder what the fuss was all about.
What I learned was considerably more complicated than I expected and quickly led to a bewildering list of innumerable types of steel and ways to treat the metal after it is produced. In this article I will attempt to review the origin of steel and the properties of some of the most important types that apply to woodworking.
All steel starts as the elemental metal, iron, which comes from iron oxide deposits in the earth (iron ore). These have been mined in vast quantities since antiquity.
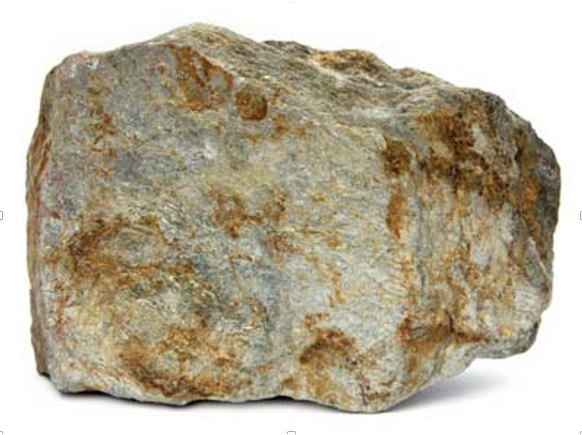
In the modern era steel is made in a Blast Furnace (invented by Bessemer in 1855). The furnace is loaded with iron ore, small amounts of flux (limestone), and coke. To make coke, coal is heated to extremely high temperature in the absence of air which drives off volatile impurities leaving pure carbon. Air or pure oxygen heated to about 1200°C is blown into the furnace. The coke burns, producing enough heat to liquefy the iron and carbon monoxide which reacts with the liquid iron, creating a solution of iron and carbon. A tap at the bottom of the furnace is opened. Molten metal pours out. The flux with impurities (slag) floats to the top. The whole process, greatly simplified here, is called smelting.
In the modern era steel is made in a Blast Furnace (invented by Bessemer in 1855). The furnace is loaded with iron ore, small amounts of flux (limestone), and coke. To make coke, coal is heated to extremely high temperature in the absence of air which drives off volatile impurities leaving pure carbon. Air or pure oxygen heated to about 1200°C is blown into the furnace. The coke burns, producing enough heat to liquefy the iron and carbon monoxide which reacts with the liquid iron, creating a solution of iron and carbon. A tap at the bottom of the furnace is opened. Molten metal pours out. The flux with impurities (slag) floats to the top. The whole process, greatly simplified here, is called smelting.
Carbon remains mixed with molten iron as an alloy (pig iron). When the carbon content is between 2% and 6.67% cast iron is produced. It can also be made by re-melting pig iron, scrap iron, steel, limestone and coke. In this process phosphorus, sulfur and carbon may be burnt out of the molten iron and carbon must be replaced. Cast iron can't be bent, stretched or hammered into shape but is easily machined.
Wrought iron is produced when carbon content is kept very low but other impurities remain. In contrast to cast iron, it can be worked by rolling, hammering or bending. In modern times it has been replaced by mild steel.
When carbon content is kept between 0.5% and 1.5%, steel (much harder and less brittle than cast iron) is produced. High carbon steel for woodworking blades is at the upper end of that range. The chemistry of steel making gets extremely complicated at this point, involving microscopic phase changes, balance between temperature and carbon content, crystal structure, melting points, etc. For a good summary of the process, check this link.
http://www.threeplanes.net/toolsteel.html
Alloy steels are made by adding one or more of many different elements to the furnace: e.g. manganese to reduce brittleness, silicon to increase strength, chromium to increase resistance to corrosion (over 12% chromium makes stainless steel), tungsten to increase hot strength for high speed tools and other elements too numerous to mention. There is no steel in carbide which is actually a compound of tungsten and carbon made by compressing powdered material at very high temperature with cobalt as a binder.
After molten steel solidifies we tend to think of it as an inert substance. But the molecular structure and physical properties of solid steel can be altered by various additional treatments. Forging: Hammering, compressing or rolling heated steel, changing the grain structure from coarse to fine and greatly increasing its strength.
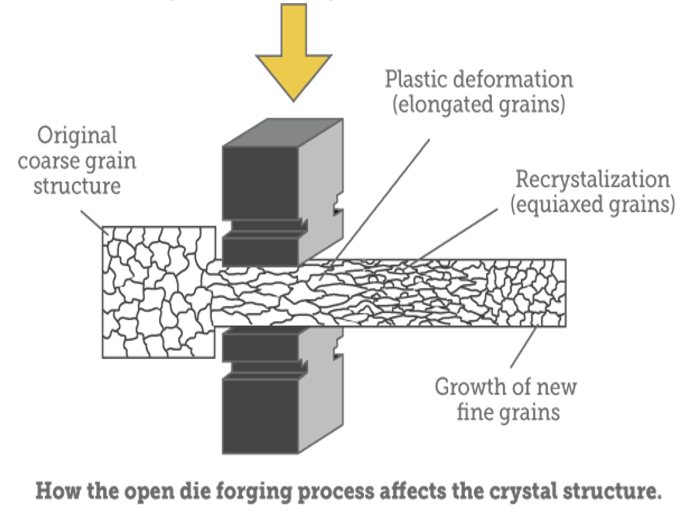
Annealing: Steel is heated to its hardening temperature, then cooled slowly to room temperature by burying it in an insulating medium such as lime or vermiculite. This softens steel for working. Hardening/Quenching: Steel is heated to its hardening temperature, then cooled either suddenly by quenching in water or an oil bath or slowly in air. Tempering: Hardened steel is reheated to its tempering temperature. This relieves stress induced in the hardening process and decreases hardness in exchange for toughness. Untempered, hardened tool steel is nearly as brittle as glass. Cryogenic treatment: Steel is cooled to as low as minus 330°; a radical form of quenching which changes the molecular structure of steel and increases both hardness and toughness. In chemical language, a process that converts the austenite phase of steel to the martensite phase (see below), significantly increasing wear resistance. Changing details of all these processes (temperature, length of time at each step, choice of material used to quench, agitation) influences qualities like shear resistance, compressive or tensile strength, ductility and wear resistance.
Steel alloys for woodworking are: O1 tool steel: “O” for oil quench, the most common tool steel. Ron Hock uses it for his high carbon blades – “a simple high carbon tool steel with very little added other than 1.1% manganese……that allows the steel to harden with an oil quench……reducing the thermal shock that occurs when orange hot steel is plunged into water”. A2 tool steel: “A” for air quench, differs from O1 steel with the addition of 5% chromium and 1.1% molybdenum, allowing it to quench in still air. This replaces oil hardening when safer hardening, less distortion and increased wear resistance are required. A2 steel also responds well to cryogenic treatment with excellent edge retention. Lie Nielsen uses the cryogenically treated version of A2 steel for bench planes and chisels. PMV11 tool steel: Introduced by Veritas in 2012, this proprietary alloy is created with powdered metal and said to be superior to all other woodworking blades. I have a shoulder plane with a PMV11 blade. It is the sharpest, most durable blade I have ever used. It was reviewed in FWW and Popular WW in October, 2012. Japanese tool steel: traditionally called White steel (Shirogami) or Blue steel (Aogami), terms that simply refer to the color of the maker's wrapping paper. White steel has no added alloys other than carbon causing a narrow hardening temperature range, requiring a high level of skill and leading to an excellent edge. These high quality blades overcome brittleness by lamination; hammer welding a layer of soft steel to a layer of harder edge steel. Blue steel is alloyed with tungsten and chromium, producing a longer lasting but not as fine an edge. The quality (and price) of Japanese blades, more than any other, depends on the maker's skill and reputation. Some master Japanese tool makers use steel salvaged from anchor chain recovered from old ship wrecks. I was skeptical about this practice until I learned about the austentite-martensite conversion in steel making, the basis for the processes of annealing, hardening and tempering (see the link below).
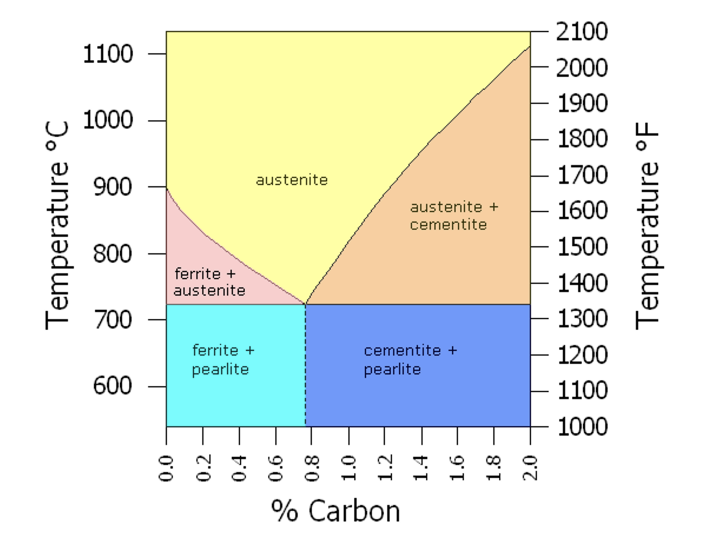
http://www.threeplanes.net/toolsteel.html
The same phenomenon occurs naturally over many decades in old anchor chains, reproducing the modern cryogenic process. Damascus steel: A legendary process invented in India around 600 BC, it results from repeatedly forge welding thin sheets of high and low carbon steel, producing an attractive pattern of swirling light and dark areas. The process was exported to China and Arabia in the 5th century and used to make swords and daggers. Attempts to reproduce the effect in modern times, more for artistic purposes than tool making, have had mixed results.
This all boils down to the fact that the choice of steel for chisels, plane blades, machine tools, saws, knives, etc. is a matter of balancing different qualities, not always mutually compatible. Hardness: resistance to permanent deformation (Rockwell scale). Hardenablity: Suitability for hardening by tempering, quenching, etc. Strength: resistance to applied force. Ductility: ability to bend without breaking. Toughness: resistance to fracturing on impact. Sharpness: precision and quality of the cutting edge. Edge retention: ability of the blade to hold an edge. Corrosion resistance: resistance to rust or stain on exposure to environment. Wear resistance: ability to resist abrasion during use. Manufacturability: ease with which steel can be tempered, shaped, machined, ground or formed. Trade offs are required; sharpness for durability, wear resistance for ease of sharpening, etc. and no one steel can meet all these requirements. But that's what makes life interesting.
By Dick Ugoretz (originally published on April 2017)
Editor's Note: Light edits have been made to remove broken web links.